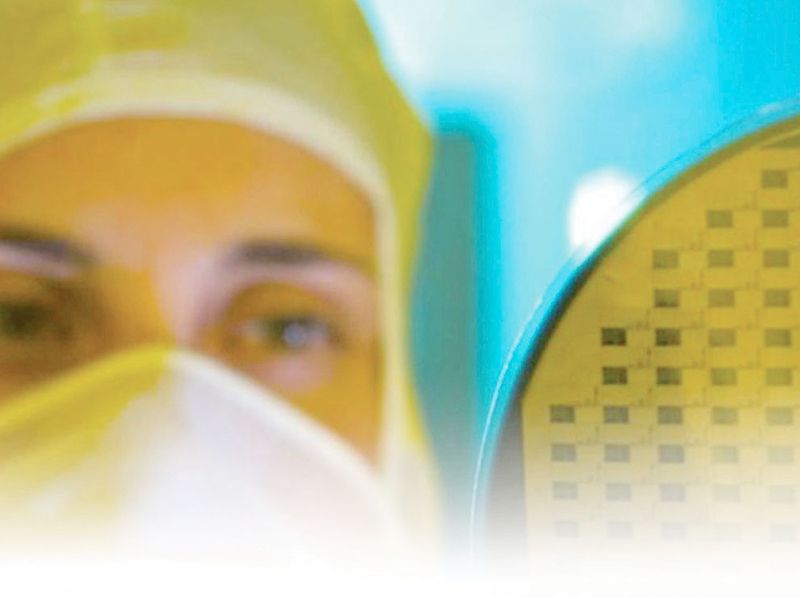
The global microchip shortage cost the auto industry millions of lost vehicles and billions in lost revenue last year. The latest estimates have the problem lingering through the first half of 2022.
To understand why the problem is now stretching into its second year, and why the industry’s urgency to fix it hasn’t delivered results, take a closer look at why it’s all so complicated.
European chip supplier STMicroelectronics, the French-Italian semiconductor maker that is Europe’s second-largest after Germany’s Infineon, is moving aggressively to address the world shortage. STM is investing up to $3 billion into its new fabrication plant, or “fab,” in Agrate, Italy, near Milan.
But semiconductor plants are slow to build, hugely expensive, complex to operate and compared with the mass-production assembly lines that automakers are accustomed to, only modest in their output. Agrate is no exception.
A vehicle plant normally works two production shifts, five days a week, for a total of 10 shifts. That number can be increased to as many as 21 shifts if an automaker needs to boost production by adding night and weekend shifts.
By comparison, STM’s chip plants are, or will be once completed, operated 24 hours a day, 365 days a year, leaving little or no room to boost output.
A new car plant can go from groundbreaking to start of production in two years, and reach full capacity in as little as six months. That same process at a chip plant takes up to five years.
And while it takes 15 to 30 hours to build a vehicle, it takes five months to produce, package and ship a chip to an automaker for installation in a vehicle.
That’s the bad news.
The good news is that in response to the worldwide shortage, chipmakers have accelerated their pace of investment to meet the auto industry’s needs. The crisis has forced more direct communication between automakers and chipmakers. And it has brought home the attitude that chip fabs should be capable of providing microchips that can meet the more advanced technological demands of vehicles that will be fully or partially electric and constantly connected.
Taiwan Semiconductor Manufacturing Co., or TSMC, began building a chip factory in Arizona in June. That company, which supplies nearly a fourth of the world’s chips, plans to spend $12 billion on the new U.S. project. But it will be 2024 before it begins to yield chips. TSMC is reportedly also now discussing the possibility of constructing a new fab in Germany.
At the same time, South Korean electronics leader Samsung is now planning to invest $17 billion in a new chip plant in Texas. And U.S. chipmaker Intel broke ground in September on a $20 billion chip capacity expansion in Arizona.
To improve chip supplies, STM is building a 12-inch fab, which will allow the supplier to increase the number of chips per wafer by a factor of 2.4 while improving process productivity.
STM’s manufacturing and quality boss, Orio Bellezza, said the new fab will rely heavily on automation, which significantly reduces staffing needs. The company started investing in the new plant in 2018, before the industry was caught up in the 2021 shortage and supply line crash. STM set out on the project both to keep up with a forecast increase in demand and to improve its own manufacturing efficiency.
The construction phase is a long one, and in Agrate, it was longer than usual. The plant is being built on land where older industrial buildings first had to be relocated. Pandemic-related operating problems added further schedule delays.
The construction phase is almost completed and the new fab just received the first batch of machines for a so-called clean room that is as big as a soccer field. The clean room is where the silicon wafers are turned into chips.
Bellezza said the first wafer will be produced by the end of the first quarter of 2022, with volume production starting by late 2022. Chips are mass-produced in silicon wafers. A single wafer comprises up to 1,000 chips.
But automotive customers, who require a longer qualification process for their semiconductors, will have to wait until late 2023 to get chips delivered from the new plant.
Then, starting in 2024, STM will begin expanding the new fab — nearly doubling its 91,000-square-foot clean room to 161,000 square feet, depending on future demand. STM expects the expansion to take until 2025 or 2026.
Once Agrate’s first production phase is completed in 2024, plant investment will have reached $2 billion. The figure will rise as the company builds up additional production modules to progressively increase capacity in line with market demand, Bellezza said.
The new fab will be entirely automated and employ between 700 and 800 operators in the first phase, and then additional workers when more clean room space is added, Bellezza said. By comparison, STM’s existing fab employs 1,400 operators and has a total work force of 2,400 people, including quality, logistics, maintenance and some production staff.
But the upgrade to a 12-inch fab does not leave the auto industry’s other product needs unaddressed. STM’s current 8-inch fab produces chips for airbags, navigation systems and keyless entry. The fab’s output will include chips for analog and radio-frequency products for vehicles with the hopes of relieving backlogs created by the shortage.
One point that is confounding the quest for more capacity is that chip customers are pushing in two conflicting directions.
For the consumer electronics and personal computer industries, two key factors changing chip production are miniaturization and increased efficiency. But for automotive customers, the factors are longevity and the ability to operate under extreme conditions. That’s partly why Europe, where the share of chip production for automotive is higher than in other parts of the world, has no fabs in the miniaturization sector — meaning below 10 nanometer. A nanometer equals one billionth of a meter, and the lower the number the better, because less distance between transistors of a central processing unit improves efficiency.
STM’s most advanced plant is a 28-nanometer fab in Crolles, France, where chips are manufactured for a number of automotive applications including vision processors for Mobileye and next-generation microcontrollers.
STM’s automotive customers are not asking it to make fabs with nanometer capabilities of 10 or below, but demand does exist for that level of expertise. Currently, STM’s European home market doesn’t have it.
In a report on the market outlook, international consulting firm Kearney said: “Today’s applications built on mature node semiconductors will, over time, move to more advanced nodes purely because of the advantages that a more advanced node technology will have for any semiconductor application; for example, reduced power consumption, higher density, etc.”
But STM decided midway through the last decade that it would quit the race to produce in-house chips with even greater circuit miniaturization. Its main reason was the huge upfront cost of the investment: up to $20 billion, according to Kearney, for a single fab that can produce 35,000 wafers a month at 5 nanometers.
As a result, fewer than a dozen plants with that capability are in operation, in places such as the U.S., Israel, South Korea and Taiwan, according to Kearney. Those locations have fabs that are producing at 10 nanometer nodes or less.
The high-stakes nature of the investment has been a problem.
In 1998, Europe produced 22 percent of the world’s semiconductors. In 2019, it produced just 8 percent, industry association Digital Europe said. It blamed the decline on the willingness of other regions of the world to introduce “a more favorable business climate.”
According to Kearney, the potential long-term cost of a 5 nanometer wafer fab investment in Europe is 33 percent higher than in South Korea, and 43 percent higher than in Taiwan. And 80 percent of the reason for those gaps is the generous incentives of the Asian governments, it reported.
In September, the European Commission stepped in with its proposal of a “Chips Act” to promote research and local production, with the target to bring the European Union’s share back to 20 percent. One possible hurdle: EU competition rules forbid state aid be used to defer costs during the chip production phase. Only research and pilot production incentives are allowed.
A directive is expected to be formally proposed in 2022, but any change of the rules will be subject to approval by all 27 EU countries.
Meanwhile, some in the industry are looking for ways around the capacity crisis by doing things differently. A growing number of automakers and Tier 1 suppliers are re-engineering automotive chips, such as electronic control units, to get more flexible solutions that can also be produced in 12-inch fabs, Marco Monti, head of STM’s automotive group, told Automotive News Europe, a sibling publication of Automotive News.
Automakers have also started buying computer chips directly from manufacturers. That’s a big change. In the past, chipmakers were considered strictly Tier 2 suppliers that provided their products to Tier 1s, such as Robert Bosch or Valeo, to build into larger components for automakers.
Daimler purchasing executive Markus Schäfer said Mercedes-Benz’s parent is talking directly with its chip suppliers, including wafer producers in Taiwan. Volkswagen Group CEO Herbert Diess said his company now has “strategic partnerships” with manufacturers in Asia.
The question for the new year is how quickly such changes in purchasing routine, technology and chip production processes will bring industry relief.