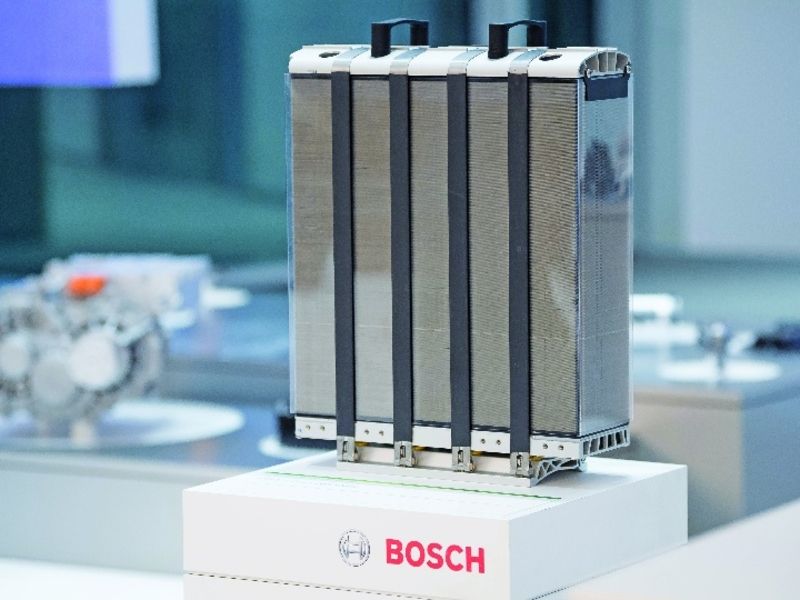
Bosch says it is making headway on one of the key barriers to the auto industry’s adoption of hydrogen fuel cells: the high cost of manufacturing them.
Producing fuel cells is expensive largely because of the cost of hydrogen — especially the sourcing of green hydrogen, according to the German megasupplier.
To offset that expense and bring down the cost of the emerging technology, Bosch is focusing its efforts on its manufacturing processes. The company is devising new production efficiencies in how the chemistry of the cells is managed, how metal is processed and how the units will be assembled.
The company is not revealing details of its factory innovations yet. But they will be critical in making the fuel cells more affordable, said Sujit Jain, regional president of powertrain solutions for Bosch North America.
“If one is looking to have a CO2-free society down the road, then it behooves us to make sure that the hydrogen that is used is also green hydrogen,” Jain told Automotive News. “The supply and the cost of green hydrogen needs to come down.
“That’ll be a big, big enabler for massive application of fuel cells in the market,” he added. “Once you have the most efficient fuel cell to begin with, and extremely high-power density in a fuel cell, it helps us in reducing the consumption of hydrogen.”
Driven by industry demands for less-expensive fuel cell technology, and bolstered by CO2 reduction targets across the globe, Jain is optimistic about Bosch’s progress.
“As the market scales up after starting in commercial vehicles, we will see the fuel cells also making entry in the passenger-car area. With economies of scale, the costs will come down, and it will be become a viable solution for passenger cars as well as trucks,” Jain said.
Bosch is developing the fuel cell stacks in partnership with PowerCell Sweden AB, in which Bosch acquired an 11.3 percent share in 2019. The products could make it to the commercial vehicle industry as early as next year.
“This is around the corner now because there is a lot of pull from our customers towards fuel cells for commercial vehicles, and that is motivating us to speed up our entry into this business,” he added. “We think that fuel cell is a major market opportunity.”
Tackling the factory cost issue also has design implications, just as it does in bringing down production costs on Bosch’s internal combustion engine products.
Bosch knows it must first assure customers that the fuel cells answer driving-range concerns, especially since the initial products are likely to be in heavy-duty, long-haul trucking.
But when it comes time to take the technology to other types of vehicles, rather than absorbing additional development costs to create separate fuel cell stacks, Bosch is relying on modularity and scalability, Jain said.
“We don’t need multiple stacks,” Jain said. “That was the thought behind it when we were developing the stack: We should design it in a way it could be modular. It is scalable so we can combine more than one stack to meet the power requirements of an entire range of vehicles.”
Jain said the company will be working continuously on the design in pursuit of lower costs.
“We are doing a continuous improvement, looking to see how we can further tweak the chemistry to get more power output of a single fuel cell.”