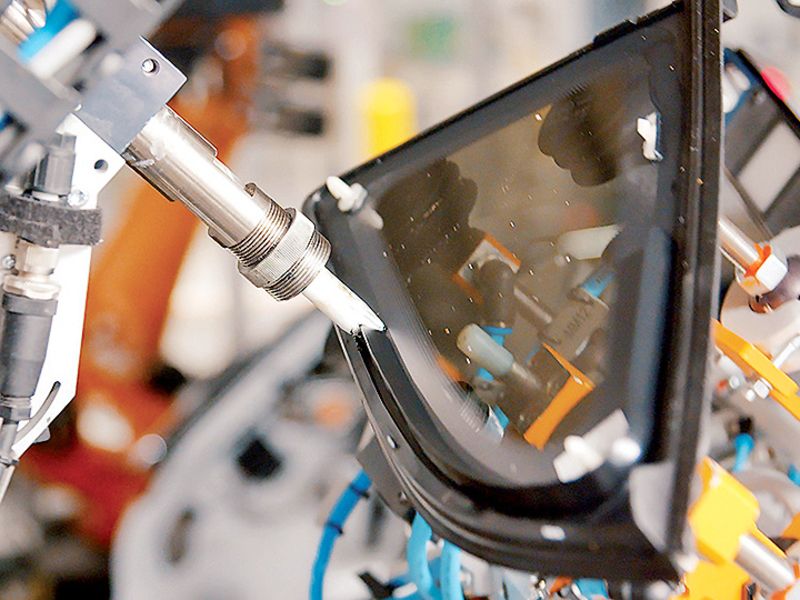
A critical product line is coming to life at Volkswagen’s plant in Zwickau, Germany, and the last thing the company wants there is a manufacturing process that holds back speed.
The product: the ID4, Volkswagen’s first all-electric crossover. The potential problem: offlining vehicles to install their windows.
To avoid that, VW turned to mechanical and plant engineering firm Dürr. For its part, Dürr turned to a whole new manufacturing process.
Volkswagen is transitioning the factory into a dedicated source of electric vehicles. The goal is to accelerate output to 330,000 EVs a year. To get there, the site is undergoing automation improvements to accommodate the unique needs of new EV architectures, with many of the changes being supplied by Dürr.
“Increasing international competitive pressure and changes in vehicle architecture, especially with regard to new drive concepts, are forcing manufacturers to exploit any potential for automation and efficiency enhancement,” Manuel Vogl, key account manager, application gluing systems at Dürr, said in a statement to Automotive News.
One innovation was Dürr’s Next.assembly strategy, which employs a new gluing technology that installs vehicle side windows in a flow process. A more traditional line would have required a stop-and-go setup for workers to spend more time at each vehicle.
To do it, Dürr had to time components and machinery to precisely line up.
First, the car body moves on the skillet conveyor assembly platform. Mounting robots guide the side window to the application tower for glue. The robot is then synced up with the platform system from a “defined trigger point,” in Dürr’s words, meaning the exact position of the body that is optimal for installation.
The side window is installed with an accuracy of a few tenths of a millimeter using this system, Vogl said.
The process does not make the assembly line move faster — it simplifies a task that would have slowed it down.
Dürr has implemented other time-saving tools in Zwickau. Its eight X-gun multidirect screwing systems hold up to four screws in a magazine and fasten them one after another, installing 26 screws a minute.
“The technical advancement of individual technologies,” Vogl said, “has now enabled these innovative and complex overall systems to be implemented and installed.”