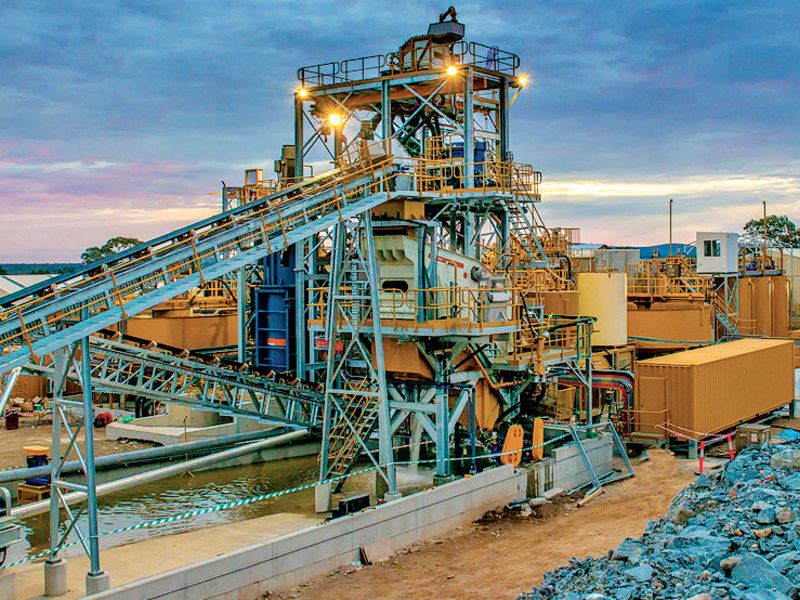
Cobalt is rapidly becoming the kryptonite of the electric vehicle revolution.
The lustrous metal has been a critical part of lithium ion batteries since they were developed and commercialized in the 1980s and 1990s. But cobalt is relatively scarce, and mostly the byproduct of copper and nickel mining. Moreover, the boom in cobalt demand has fueled a rise in child labor and dangerous working conditions for small-scale miners in the cobalt-rich Congo.
“Cobalt is considered the highest material supply chain risk for electric vehicles in the short and medium term,” according to the U.S. Department of Energy, which is funding research and development on alternatives. “The United States does not have large reserves for cobalt, and the extraction and early-stage processing is concentrated in a small number of countries.”
Media coverage of children toiling under appalling working conditions in Congo — the world’s largest cobalt producer — has transformed the metal into the “conflict diamonds” of the EV age. Cobalt also is increasingly expensive and composes a relatively small part of the modern EV battery, making it ripe for elimination by more abundant metals.
But cobalt is critical. It serves as a stabilizer in the cathode of high-energy batteries and allows for relatively high energy density while helping to prevent uncontrolled discharge that can cause battery fires.
Fortunately, there are cobalt-free batteries already on the market and intense research into future versions is taking place. Most automakers and battery producers are moving away from cobalt as quickly as they can by reducing the amount in new chemistries. Overall demand for cobalt will remain high as battery production multiplies, but alternatives will ease supply concerns, according to mining forecasters.
Chinese automaker BYD has been using proprietary lithium-iron-phosphate batteries because of their low cost in the highly competitive local market. Iron is plentiful compared with cobalt, nickel and other metals used in EV batteries. The lithium-iron chemistry is often referred to as LFP for lithium ferrophosphate. BYD has a bus factory in Lancaster, Calif.
Tesla has been using LFP batteries for its China-made vehicles through a contract with battery-maker CATL, according to Reuters. Tesla recently started introducing them into production at its plant in Fremont, Calif. In October, Tesla said it will shift to LFP chemistry for all of its standard-range vehicles globally in a massive shift away from cobalt.
The downside to lithium-iron batteries is their low energy density, although that also increases their stability and safety. But there also are a variety of high-energy batteries with cobalt-free chemistries under development.
One project at the University of Texas at Austin has created a cobalt-free battery that is 89 percent nickel, with the remainder manganese and aluminum. The prototype has a higher energy density than current batteries that use cobalt, and the project has generated a Houston-based startup, TexPower EV Technologies, to commercialize the technology.
“When you increase the nickel and reduce the cobalt, you achieve two things together: longer EV driving range and lower global costs,” said Arumugam Manthiram, director of the Texas Materials Institute and Materials Science and Engineering Program at the university. He also is a partner in the TexPower startup, along with two students who worked on the project.
Manthiram told Automotive News that he’ll continue to push the limits of the battery chemistry to hopefully reach 100 percent nickel. The pure nickel cathode will require some innovations to be as safe as cobalt formulations.
“All of the batteries have some safety issues,” Manthiram said. “But that can be controlled by how the cell is designed and software controls.”
Manthiram said LFP batteries are an important development in terms of cost and safety. But their low energy density makes them mostly useful for vehicles with modest range and price. As they stand now, LFP batteries are not going to provide 500 miles of range or be appropriate for larger, American-size vehicles. But they could work in some U.S. vehicles.
A lot of battery research is driven by material cost and abundance, Manthiram said. Cobalt is relatively scarce, nickel is more abundant and iron is everywhere. And research continues on sulfur, which comes from petrochemical waste, for cathodes. Sodium from the ocean may someday replace lithium itself, creating mining-free batteries.
Battery recycling also is a critical part of the equation, in hopes of reducing the desperate search for increasingly scarce resources to fuel the EV transition.
“Today, it’s a cobalt problem,” Manthiram said. “Tomorrow, it could be a nickel problem and after that it could be an iron problem. But maybe not.”