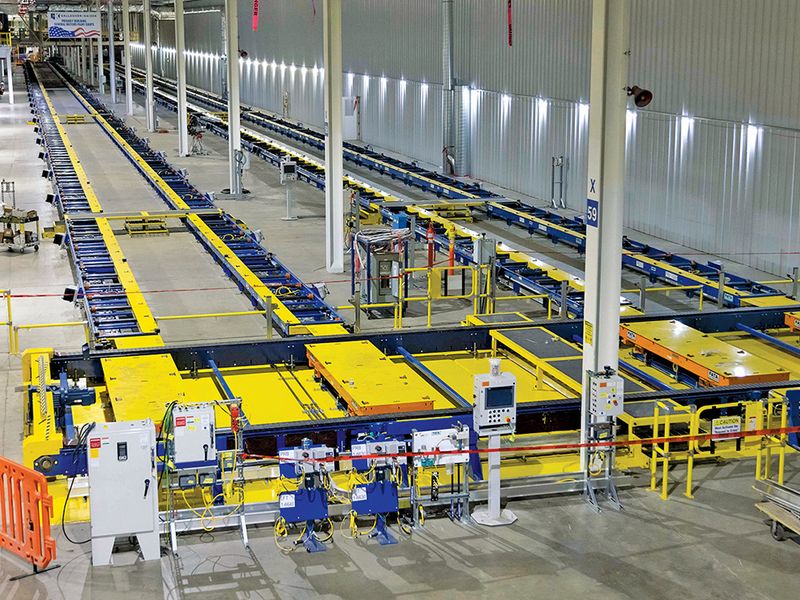
DETROIT — As General Motors begins transitioning to an all-electric light-vehicle portfolio, its manufacturing philosophy is clear: Use the assets it already has.
GM will retool assembly plants to produce electric vehicles, convert engine plants into battery facilities and build electric drive units at transmission plants to streamline and reduce the cost of EV manufacturing, said Gerald Johnson, executive vice president of global manufacturing and sustainability.
By 2025, EV production will account for 20 percent of GM’s manufacturing footprint in North America, Johnson said as part of the automaker’s presentation to investors last week. By 2030, it’s projected to be half.
Renovating existing plants, rather than building new ones, will save GM $1.5 billion per plant, Johnson said. That will total $15 billion in capital spending saved by 2030 and up to $30 billion by the time GM has converted its full lineup to battery power.
The strategy contrasts with Ford Motor Co.’s newly revealed plan to build battery plants and an electric pickup plant on two new campuses in Tennessee and Kentucky.
GM began retooling its Detroit-Hamtramck Assembly plant for EV production last year. The plant, since renamed Factory Zero, is slated to launch its first vehicle, the GMC Hummer EV pickup, this fall. GM repurposed 80 percent of the plant’s infrastructure and equipment, Johnson said.
“We didn’t build walls,” he said. “We didn’t have to create a shipping yard. We didn’t have to add utilities or building infrastructure. We already had them.”
The retooling and advanced technology updates cost two-thirds as much as an all-new plant would have, he added.
Rehabbing plants also saves time, Johnson said. Factory Zero began preproduction less than two years after its renovation started, and retooling can go even quicker at plants that will build EVs alongside gasoline-powered vehicles, such as Spring Hill Assembly in Tennessee.
Four years can pass between breaking ground on an undeveloped construction site and the start of production, and new plants require more time and resources to validate, troubleshoot and synchronize processes, Johnson said.
Another reason GM doesn’t need new plants: Much of the assembly process remains the same between EVs and gasoline-powered vehicles, he said.
No matter the propulsion system, all vehicles have seats, doors and many other common parts.
“They process through body shops and paint shops in the same amount of time,” Johnson said. “In fact, we can produce a simple EV in the same amount of working hours it takes to produce an ICE vehicle today.”