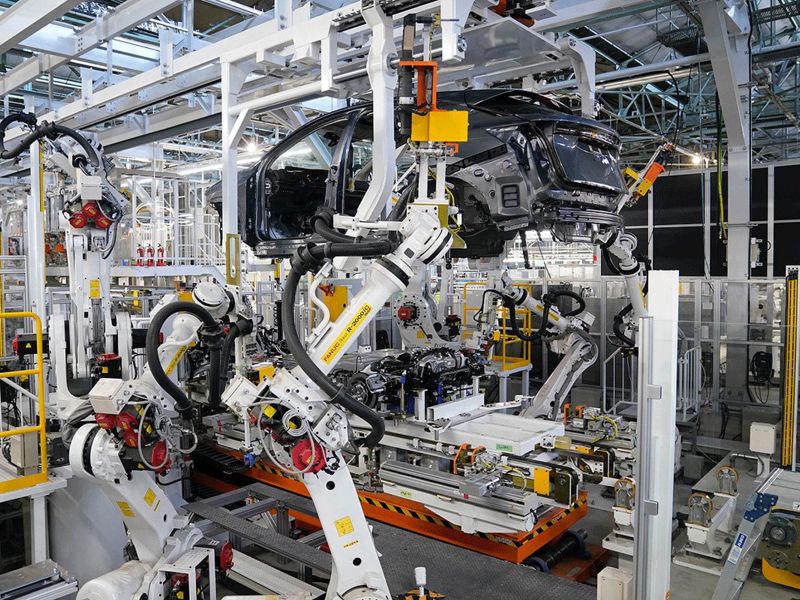
KAMINOKAWA, Japan – Nissan’s most advanced factory yet takes production of green vehicles to a higher level, delivering efficient, flexible manufacturing firepower to make next-generation EVs, including the highly-anticipated Ariya crossover.
The so-called Nissan Intelligent Factory, shown to reporters for the first time Friday, deploys a host of new production methods, including several world-first techniques, to enable a 10 percent production cost improvement over older methods, despite building more complex vehicles.
A key innovation is a new powertrain assembly technique called SUMO, short for simultaneous underfloor mounting operation. It foreshadows Nissan’s approach to next-gen EV production.
The Intelligent Factory has already begun pre-production of the Ariya at Nissan Motor Co.’s Tochigi assembly plant north of Tokyo, replacing a Line 2 that used to make some of Nissan and Infiniti’s top-tier products.
Tochigi’s Line 1 now hosts consolidated output of such vehicles as the Nissan GT-R and Z sports cars as well as Infiniti models. The all-electric Ariya is set to go on sale this winter.
The Intelligent Factory’s three-diamond logo is supposed to represent the “edgy” technologies inside. Nissan’s production engineers spent years developing the new techniques being rolled out.
The goal is to target carbon neutrality and automate production as much as possible. Robots have replaced human workers in a plethora of roles, as Nissan tries to improve productivity and quality and cope with the challenges employers here face due to Japan’s rapidly shrinking workforce.
Nissan’s overhaul comes as other Japanese automakers move to modernize their facilities for a new era of electrified mobility. Earlier in the week, Mazda Motor Corp. unveiled a similar upgrade of one of its plants in Japan to allow for flexible mixed production of electrified vehicles.
Honda has said its lineup will go gasoline-free by 2040, and Toyota is also ramping up its EV ambitions.
Nissan’s SUMO process delivers new efficiencies by mounting all of the vehicle’s powertrain components simultaneously from a plug-in palette that is lifted into the body and fitted by robots.
The front, middle and rear of the palette are made of interchangeable modules that can accommodate a multitude of layouts, for electric, hybrid and internal combustion vehicles.
At Nissan’s Oppama plant near Yokohama, where the company already uses a less-refined mixed production method to make the Leaf all-electric hatchback, workers still need to guide the drivetrain components into place and manually mount them in a labor-intensive process.
“The first mission is to break away from this traditional, labor-intensive model,” said Hideyuki Sakamoto, executive vice president for manufacturing and global supply chain management.
“We need to build a production scheme for next-generation vehicles.”
Nissan announced the Intelligent Factory in 2019, saying it would invest about 33 billion yen ($296 million) to reboot the Tochigi plant as an EV hub, making it more flexible, competitive and environmentally friendly. The result is a Nissan blueprint for future factory overhauls worldwide.
Robots are tapped throughout the Intelligent Factory to replace human workers.
They are used, for example, in a new process that installs headliners in the ceilings of the Ariya, and they are used to automatically install the vehicle’s cockpit module. With high-speed sensors and indefatigable, ultra-precise movement, the robots greatly improve quality, Nissan said.
World-first production processes include a high-speed automatic copper wire winder for the Ariya’s motor. Nissan said it is the first example of mass production for an 8-pole motor that ditches the use of permanent magnets to break the dependence on rare earth materials.
Nissan also uses a new process that integrates painting of the Ariya’s steel body and resin bumper panels into one process – cutting down time, complexity and emissions.
Before, the body and bumpers had to be painted separately because they required different baking temperatures. Now, thanks to a newly developed water-based paint that cures at lower temperatures, Nissan can paint them at the same time, cutting energy consumption 25 percent.
Nissan chalked up that breakthrough as another world’s first.
To check the paint job, Nissan has also deployed a new robot-driven automated inspection process that scans the cars with bright zebra lighting. It has the world’s finest eye for defects, Nissan said, spotting flecks of dust no bigger than 0.3-millimeters in diameter. Similar technology previously on the market could only detect defects down to the 0.5-millimeter size, Nissan said.
“This robot is actually replacing the human,” said a manager of the new paint shop. “We actually transplanted human visual recognition capacity into the robot.”
Elsewhere in the Intelligent Factory, Nissan leverages artificial intelligence, advanced connectivity and augmented reality to improve productivity.
The entire final assembly line is wired with sensors and web cameras to monitor the machines at a central control center, where engineers watch a wall of computer monitors looking for problems.
The center uses AI to predict and preempt looming breakdowns in the machines so Nissan can fix them quickly or catch glitches before they even happen.
Meanwhile, trainers have dropped textbooks and videos when bringing new employees onboard.
New teaching tools are mixed reality goggles, which combine virtual reality with augmented reality. When workers strap them on, Nissan says they not only speed up training but do a better job of making the lessons realistic and memorable for employees.